
One of the most common questions is how OEE (overall equipment effectiveness) is calculated. This article is intended to explain what that means in the context of FactoryWiz.
First off - OEE is calculated out of your scheduled time only. If you have shifts in FactoryWiz covering 16 hours per day, only those 16 hours matter. That works both ways - machines sitting idle during the unscheduled time don't drag your time down - but also machines running during your unscheduled time don't drag your score up - either. If you have machines which run unattended - it is recommended that those machines are set for a 24 hour schedule to capture all of their production within your OEE score.
With those unscheduled hours tossed out the window - the first part of OEE is the availability score. This number is akin to your "uptime". How much time out of those 16 hours today has this machine managed to stay running - that is your availability. Anything which causes the machine not to run is an availability loss. This includes unloading and loading, setup, breaks, unscheduled machine outages, insufficient staff, etc. It is important to recognize two things: this is not overall operator effectiveness. Even if there is no operator - you have a piece of equipment which has capacity and which is experiencing a loss (the loss reason being "there is nobody to run it"). Second, just because there is a loss doesn't mean someone is doing anything wrong.
On a machine with automation or automatic bar feeders - the availability score will be much higher than on a mill with short cycle times and manual loading. Some processes have long setup times. Some processes the machinery will only run for 25% of the time simply because of how the process is designed - not due to lack of hard work or motivation on the shop floor. It is important we recognize that we are simply measuring the process as it exists and have realistic expectations. What we do not want to do, however, is hide it. Frequently we are asked to build in some "fudge factor" that makes the machine appear as though it were running at 100% by hiding those losses - and that could be a useful metric in some applications but it is not OEE. Instead - we want to measure those six hours per day lost to loading and unloading because eyes off the problem is an excellent way of ensuring you will never improve it. Perhaps you could reduce that number with automation. Perhaps you want to compare your machines without automation to those with automation before you buy your next piece of equipment. Hiding the numbers to look good will lead to less informed decisions. Why should you buy a machine with automation for twice the price when your machines without automation appear to run at 95% OEE? That's why OEE doesn't fudge the numbers. It may seem brutal - but every little loss that is not the machine running gets counted and categorized for better decision making.
The next part of OEE is the performance metric. This is not your uptime. This is not how fast your operators load the machine. That is availability! Performance can be considered "is this machine running to specification". Reasons for performance losses could be an operator turning down a feedrate override or a wire EDM having a short which is causing it to cut slower. The machine is running, but it isn't producing the part as quickly as it should. This is determined by comparing the actual time versus a benchmark. A frequent question is, "why can't I just look at how long the machine is taking to run a part and use that as a benchmark?" Then both halves of the equation will be coming from the same place! In aggregate, the recorded cycle times over the recorded cycle times will always be 100%. If I run the first 100 parts at 50% feed override and the next 100 parts at 50% feed override - I still only am getting 50% of my parts per hour but the formula would show 100%. You can use FactoryWiz history to give you an idea of what the benchmark should be - but that should be a defined value which is not fluctuating with the machine cycle times, and which you have some control over. That number can be embedded into the machine's part program, stored in a spreadsheet, input manually (recommended against), or accessed via some external system such as your ERP - but that will give FactoryWiz something to compare the actual times against and come up with your performance percentage. If no benchmark time is available, performance is defaulted to 100% meaning your OEE number is really just an availability number.
Finally - quality is simple. All parts are considered good unless flagged otherwise. If an operator flags something for non-conformance, or it is later flagged by a CMM or person in QA, those will subtract from the good total and be reflected in the quality percentage.
Multiply availability times performance times quality and you get your OEE for scheduled time!
Some additional notes:
- Sometimes there are times which you would like to exclude from the OEE schedule such as planned maintenance. Set a mode for planned maintenance in FactoryWiz and configure this mode to be entirely excluded from OEE to achieve this.
- Other times, a machine may be running but not productive. For example, warmup. If a machine is warming up for three hours the light may be green but we should treat that as lost time. To do this, set a warmup mode in FactoryWiz and define that mode to always count as idle.
- Part counting is important! Even if you don't care about the part counts on the reports, the part count is another way of looking at "when was each part completed." We need to know that to have cycle times for performance, and we need a part count for quality because you can't determine a percentage unless you know how many parts were made to begin with. Make sure your programs count your parts before using either Performance or Quality metrics to get a complete OEE. Without it - you can only determine availability.
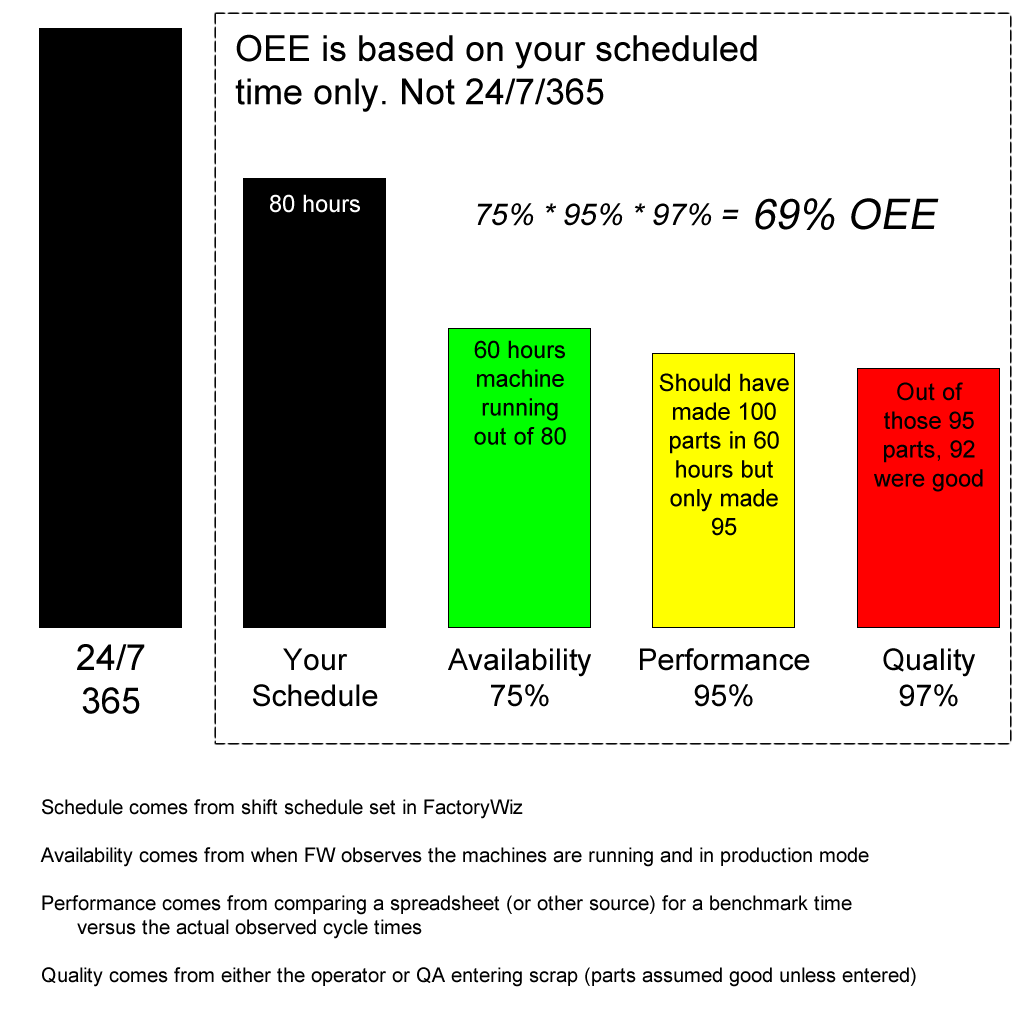
Related Articles
8.7.10 OEE Calculation
Overall Equipment Effectiveness (OEE) measures the percentage of manufacturing time that is productive. It combines measurements of availability, performance, and quality: · Availability: the percentage of the scheduled time during which the machine ...
Understanding OEE
OEE Understanding OEE Overall Equipment Effectiveness Metrics that go into the OEE formula Availability Performance Quality OEE OEE = Availability% x Performance% x Quality% if: Availability = 91% (0.91) Performance = 98% (0.98) Quality = 99% (0.99) ...
8.10.6 Machine Modes Excluded From OEE
On the Machine Modes Excluded From OEE page, you can view a list of current machine modes excluded from OEE, add new, edit, and delete machine modes excluded from OEE. You may select from a list of machine modes that have already been entered by the ...
8.10.7 Machine Modes Always Idle For OEE
On the Machine Modes Always Idle For OEE page, you can view a list of current machine modes always idle for OEE, add new, edit, and delete machine modes always idle for OEE. You may select from a list of machine modes that have already been entered ...
10.4 Data Dictionary
Overview of Database Tables FactoryWiz is an open system, meaning we give users full access to all data for the purpose of writing custom applications and reporting solutions, as well as integrating with other business applications such as ERP ...